Heat sink tutorial
Thermal conductivity
Usually a heat sink is used to spread the heat away from a
thermal source in order to reduce the temperature of the source. Typical
sources in my world are power semiconductors and power resistors.
This means that thermal conductivity is the most important
property of the heat sink. Thermal conductivity of a heat sink is a function of
cross section and the material property (thermal conductivity) of the
metal.
In metals heat is transferred though conduction electrons
and phonons. The phonon (lattice vibration) contribution is similar to that of
an insulator with the same weight atoms, so the phonons are not insignificant.
For example the thermal conductivity of aluminum oxide is 30, versus aluminum
metal at 220, so about 10-15% of the thermal conductivity is due to the
phonons. But for most of the thermal conductivity the electrons are doing most
of the heavy lifting.
Thermal conductivity of a metal depends on how far
conduction electrons, can travel without scattering. Conduction electrons can
be scattered by phonons, which is why thermal conductivity gets worse as the
temperature goes up. The more phonons traveling through the metal, the higher
the probability of having them run into a conduction electron.
Conduction electrons and phonons are also scattered by
impurities. An electron traveling through an aluminum crystal will be scattered
if it runs into an impurity atom in the lattice, such as zinc or copper, or
even an aluminum atom of a different isotope. They can also be scattered by
defects in the aluminum crystal. So if an aluminum atom is missing, or is
displaced from the crystal lattice that site will scatter electrons moving past
it.
Conduction electrons and phonons are also scattered by
interfaces. Interfaces include the edges of the metal, but also crystal domain
edges.
Here I should point out that the same thing that makes a
metal strong also lowers its thermal conductivity. A pure crystal is soft
because it is easy to slide the crystal layers over one another. Impurities and
crystal boundaries will "pin" the crystal layers to keep them from sliding.
Crystal defects introduced by deforming the metal (work-hardening) strengthen
the metal by using crystal defects to keep the atomic layers from sliding. And
will also create scattering centers to lower the thermal (and electrical)
conductivity.
So the highest thermal conductivity metals will be pure
and annealed with large crystal domains.
Aluminum heat sinks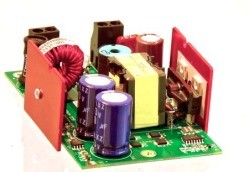 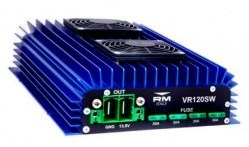 Table 1. Aluminum wrought alloys arranged by thermal
conductivity. In annealed state except 4032-T6. The strength of tempered
versions can be considerably higher than listed here. For flat stamped heat
sinks I usually specify 1100, it is one of the best for thermal conductivity,
it is readily available, inexpensive and best of all easily remembered. For
heat sinks that will need extensive machining I use 2024 or 6101.
Aluminum Alloys |
Thermal Conductivity W/(°C-meter) |
Tensile Strength MPa |
Extrudability |
Forming |
Main alloying element |
1350 |
234 |
83 |
100 |
+ |
99.5% Aluminum |
1060 |
231 |
69 |
100 |
+ |
99.6% Aluminum |
1050 |
222 |
105-145 |
100 |
+ |
99.5% |
1100 |
222 |
90 |
100 |
+ |
99.0% |
6101 |
220 |
97 |
50 |
+ |
1% Si+Mg+B |
3003 |
193 |
110 |
60 |
++ |
1% Manganese |
2024 |
193 |
186 |
10 |
+ |
4% Copper |
2017 |
193 |
179 |
10 |
+ |
4% Copper |
6061 |
180 |
124 |
50 |
+ |
2% Mg+Si+Cu |
7075 |
173 |
228 |
5 |
- |
9.7% Cu+Mg+Zn |
2219 |
171 |
172 |
10 |
+ |
6% Copper |
3105 |
171 |
117 |
60 |
+ |
1% Mn+Mg |
4043 |
163 |
145 |
|
|
5% Silicon |
4032-T6 |
154 |
379 |
|
|
12% Silicon |
2011 |
151 |
379 |
10 |
+ |
5% Copper |
5052 |
138 |
180 |
30 |
+ |
2% Magnesium |
5456 |
117 |
310 |
30 |
+ |
5% Magnesium |
8090 |
95 |
340 |
|
|
2% Li 2% Cu |
Copper heat sinks
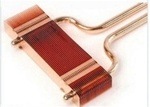 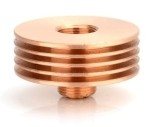 Table 2. Copper has great thermal conductivity, but add any
alloying elements to it and the thermal conductivity drops fast, as you can
expect. Two percent Beryllium cuts the thermal conductivity by 2/3.
Copper Alloys |
Thermal Conductivity W/(°C-meter) |
Tensile Strength MPa |
|
|
Type |
C10100 |
394 |
221 |
|
|
Oxygen free high conductivity |
C15000 |
367 |
255 |
|
|
0.15% Zirconium |
C18200 |
324 |
234 |
|
|
1% Chromium |
C17000 |
107 |
483 |
|
|
1.7% Beryllium |
C26000 |
121 |
338 |
|
|
Cartridge brass |
C35000 |
116 |
324 |
|
|
Leaded brass |
C46400 |
116 |
400 |
|
|
Naval brass |
C51000 |
46 |
485 |
|
|
Tin bronze |
C75200 |
33 |
414-1000 MPa |
|
|
Nickel silver |
Steel heat sinksTable 3. Sometimes sheet steel is
already in your product, and if you can get away with using it as a heat sink
it saves money and complexity.
Steel |
Thermal Conductivity W/(°C-meter) |
Tensile Strength MPA |
|
|
Fabrication |
1006 |
65 |
295 |
|
|
Hot rolled |
1010 |
52 |
325 |
|
|
Hot rolled |
1018 |
52 |
325 |
|
|
Hot rolled |
1020 |
52 |
380 |
|
|
Hot rolled |
1070 |
51 |
640 |
|
|
Cold drawn |
2205 Stainless |
19 |
750 |
|
|
Annealed |
410 Stainless |
25 |
520 |
|
|
Annealed |
316 Stainless |
16 |
586 |
|
|
Annealed |
304 Stainless |
16 |
586 |
|
|
Annealed |
Zinc heat sinks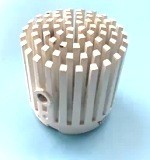 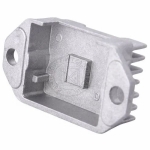
Table 4. Zinc can be die cast to make complicated shapes at
low cost and so is attractive as a heat sink. Injection molding machines are
made specifically to mold zinc just like plastic. The thermal conductivity of
zinc is moderate because it has large percentages of five different isotopes
that cause electron scattering. Because of this the thermal conductivity
doesn't change much when small percentages of alloying metals are added.
Zinc |
Thermal Conductivity W/(°C-meter) |
Ultimate Tensile Strength MPA |
|
|
|
Pure Zinc |
125 |
145 |
|
|
|
Zamak 3 |
113 |
268 |
|
|
4% Aluminum |
Zamak 5 |
108 |
331 |
|
|
4%Al 1%Ci |
KS |
105 |
200 |
|
|
4%Al 3%Cu |
|